pVARD and SensorSub Technology
About
DTL Field Trials of Passive Vibration Assisted Rotary Drilling
Vibration-Asssted Rotary Drilling (VARD) and SensorSub are drilling technologies developed in collaboration with Husky Energy (now Cenovus Energy) and Suncor Energy with funding from the ACOA Atlantic Innovation Fund (AIF) of the Canadian Government and the Industrial Research and Innovation Fund (IRIF) of the Newfoundland and Labrador Government. The VARD technology enhances rotary drilling penetration rates in combination with reducing drill bit wear and damages, and has been awarded several patents. The SensorSub is a Measurements While Drilling (MWD) tool which records drill string rotation and tri-axial drilling vibrations with high sampling rate to enabling high fidelity analysis and modelling of drill string motions and vibrations. Both technologies and developed and tested at the Memorial University Drilling Technology Laboratory (DTL) where reduced scale prototypes were tested in physical drilling simulators as shown in Figure 1. Assisted using modelling and simulation, field-scale versions of the drilling tools were developed from these laboratory prototypes.
Figure 1: Drilling researcher Dr. M. Mokhtar Said standing next to the Large Drilling Simulator a physical drilling simulator at the MUN Drilling Technology Laboratory capable of simulating drilling under a range of downhole dynamic and pressure conditions.
These field-scale tools were evaluated using field drilling trials (Figures 2,3, and 4) where drilling was conducted in multiple parallel wellbores over a 200 m vertical interval of interbedded shales and quartz-veined shale with various VARD and non-VARD bottomhole assembly configurations.
Outcomes:
Results of the drilling trials indicated that when the VARD tools were operated within the operational range of the tool (as previously determined from numerical simulations and lab-scale prototype testing) drilling penetration rates were higher using VARD compared to non-VARD drilling as shown in Figure 5. Drill cuttings collected throughout the drilling trials were also larger for VARD drilling compared to non-VARD drilling. Analysis of SensorSub data confirmed that dynamic actions of the VARD tool occurred during the periods of increased penetration rates and larger drill cutting size, confirming the enhanced VARD penetration mechanisms.
Figure 2: Field drilling trials conducted at Greenslades Quarry near St. John’s, NL showing the rotary drilling rig, pumping unit, supporting equipment and vehicles, and the drilling tools in the foreground.
Figure 3: Mobile laboratory set-up to assist with configuring the VARD and SensorSub tools (shown in the inset) over the duration of the field trials.
Figure 4. Drilling Bottom-hole Assembly (BHA) showing the VARD and SensorSub tools relative to the PDC drill bit.
Figure 5: Plots of drilling Rate of Penetration (ROP) as a function of Weight-on-Bit (WOB) for drilling the same formations with VARD (pVARD) and non-VARD (CONV) drilling configurations. Within the tool operating range of approximately 60 to 110 KN WOB, VARD drills 20% to 60% faster than non-VARD.
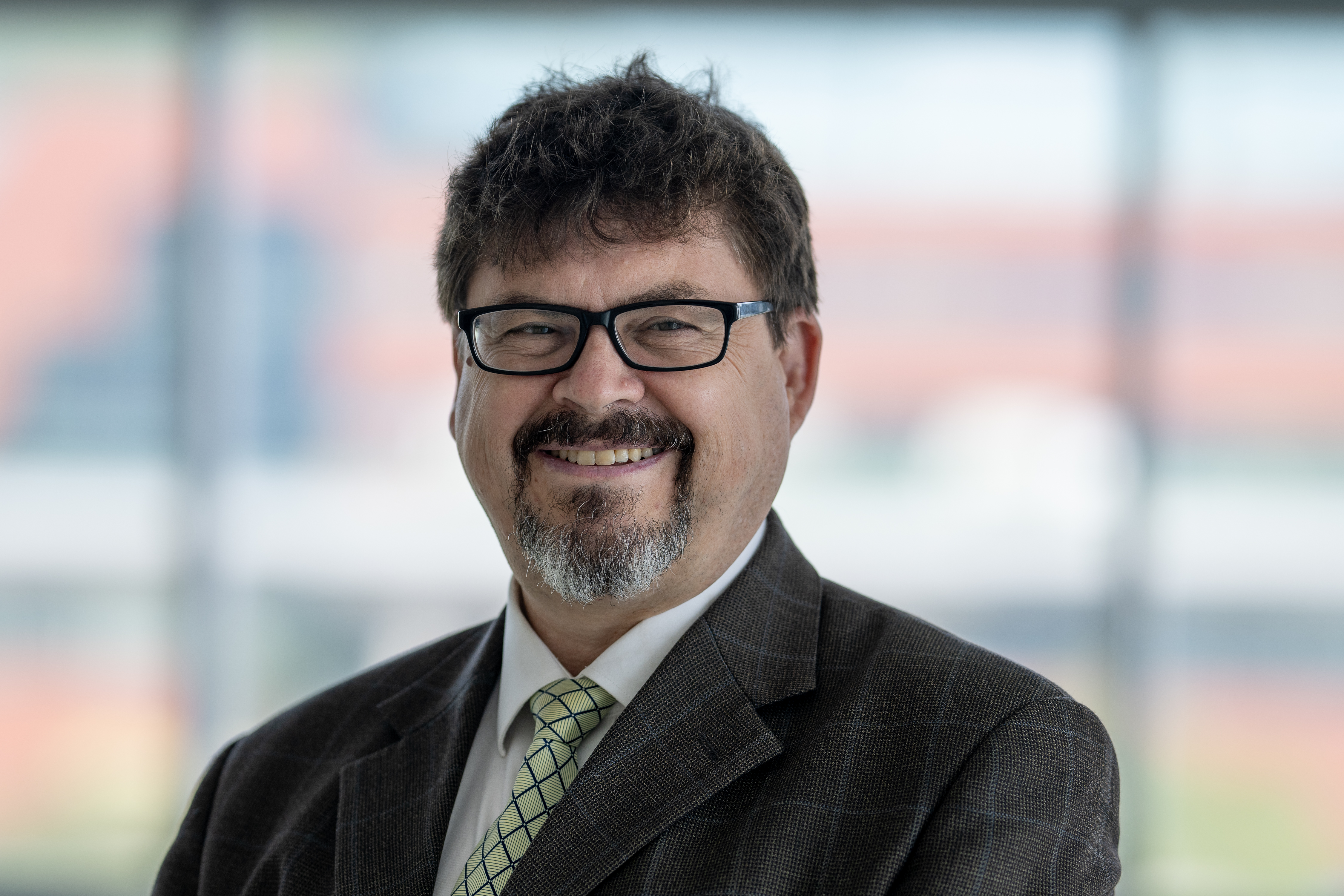
Investigators
Dr. Stephen Butt
Dr. Stephen Butt is a Professor of Process Engineering engaged in the sustainable development of natural resources through teaching, research and industry collaboration. His research includes drilling technology development to improve drilling penetration mechanisms and performance, high resolution subsurface imaging based on seismic and electro-magnetic wave propagation, and reducing environmental footprint for mining operations through development of highly selective mining methods and technologies. He leads the MUN Drilling Technology Laboratory where he has held research funding of $6.5M CAD as Principal Investigator, $13.5M CAD as Co-Investigator, supervised ~120 Highly Qualified Personnel (HQP), published ~240 articles and proceedings, and holds several patents.
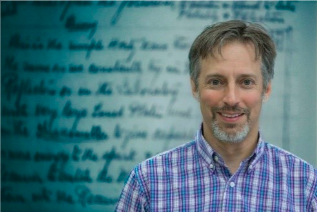
Dr. Geoff Rideout
Dr. Geoff Rideout is a Professor of Mechanical Engineering engaged in teaching and research is areas of dynamics, vibrations, design, and modeling and simulation. His research is includes methods to partition simulation models to decrease computation time, developing a suite of models of varying complexity to predict multi-mode vibrations in oilwell drillstrings, dynamic control of vehicle suspensions to improve ride quality and safety, and developing NDT methods for wood poles based on modal impact testing. He has worked in industry as a manufacturing process and design engineer, has received several awards for distinguished teaching, and is currently the Head of Mechanical Engineering.
Partners
Contact
Faculty Member |
Contact Info |
Dr. Stephen Butt |
Phone: 709-864-8955 Email: sdbutt@mun.ca Office: EN2110D |
Dr. Geoff Rideout |
Phone: 709-864-3746 Email: g.rideout@mun.ca Office: EN3017 |
Faculty of Engineering and Applied Science
Memorial University of Newfoundland
St. John's, NL